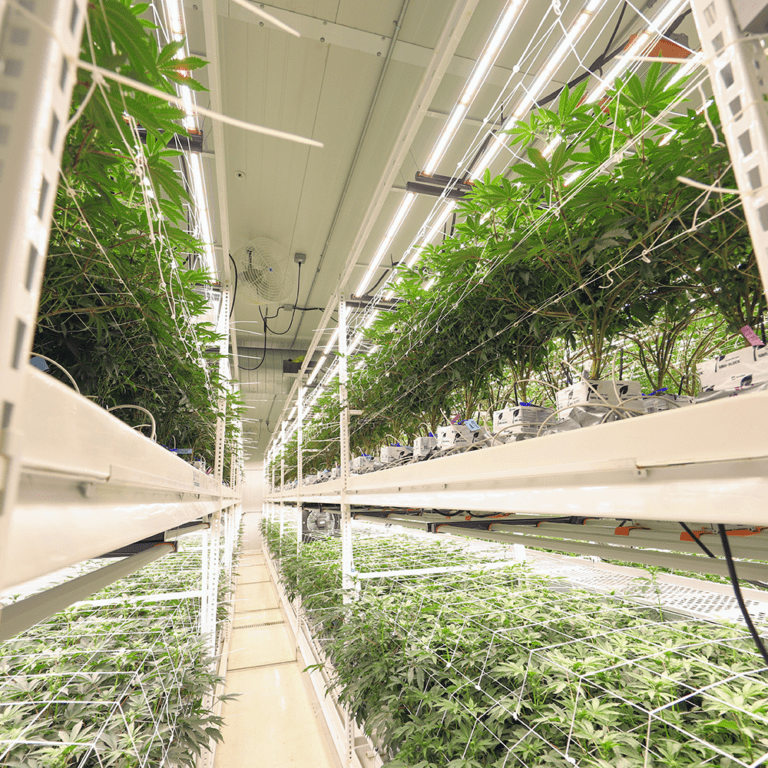
When cannabis first emerged as a leading agricultural product, single-tiered cultivation methods evolved quickly to keep up with consumer demand. Stationary facilities became fully mobile while adding tiers to accommodate vegetative and flower production.
Cultivators jumped at the opportunity to rewrite SOPs and increase efficacy without compromising yields. How could they transform their facilities for optimized profit and real-world success?
The answer is simple: embrace purpose-built vertical farming technologies and determine the best ways to use them. Over the past few years, the refinement of LED lighting, airflow solutions, fertigation guidelines, and HVACD controls has empowered growers to produce COAs and yield metrics once considered unattainable.
These amazing results are a byproduct of proper planning, understanding mechanical, electrical, and plumbing systems, preparing for SOP refinement, sourcing quality genetics, and using efficient solutions to make the most of investments and the space available.
Multi-tier cannabis cultivation might seem intimidating. However, with careful design, good partners, and the appropriate tools, you can transition to multi-tier growing or build a new facility from the ground without hesitation.
Let’s explore six key factors to consider as you take your cultivation operation to the next level.
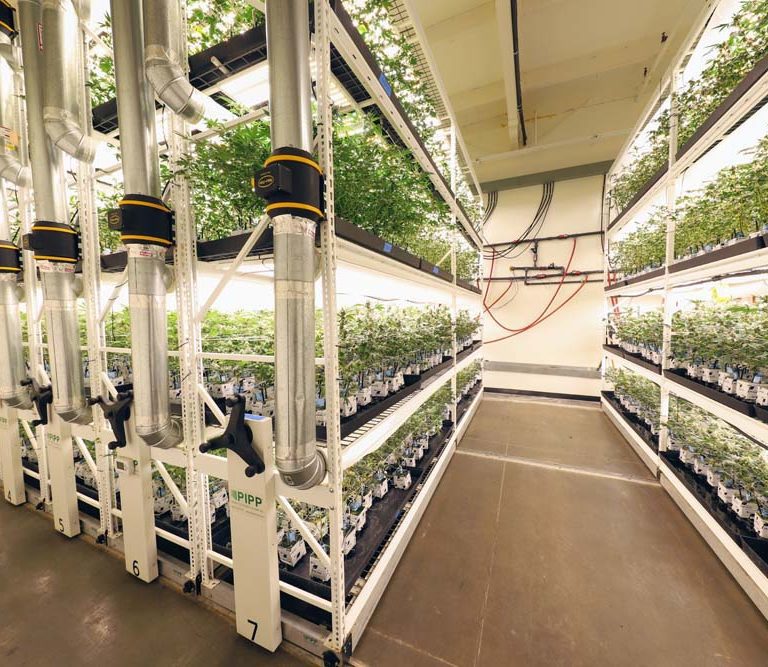
1. Have a Solid Plan
Executing a new infrastructure requires effective planning in any industry but is especially necessary when cultivating cannabis. When transitioning to a vertical farm, growers must understand the biggest limiting factors of their success.
Working collaboratively with equipment experts like Pipp Horticulture can ensure a seamless transition to vertical cultivation. Our team will help you choose a racking design and layout that aligns with your unique space and production requirements.
For example, we can provide a total canopy number per room, allowing you to estimate lighting, HVACD, plumbing, fertigation, and electrical needs. These insights will help you create an accurate timeline and budget for your project as you move through the process.
Here are a few questions to ask when converting to a vertical farming system:
- Do I have adequate electric capacity?
- Is my building structurally sound enough to install HVACD on the roof?
- How much extra dehumidification performance will I need?
- What is the best light for my tier spacing?
- How am I going to move air through the racks?
- Can I ramp up propagation or clone orders to meet demand?
- How big will my plants be?
- How will my team access the second tier?
- Which Standard Operating Procedures (SOPs) will I need to adjust?
- What additional airflow solutions should I consider for each space?
- Will we need more space for curing?
2. Make Checklists
Visit each department in your facility–from your cloners to harvesters. Talk to them about the impact of going multitier. What metrics and KPIs are most likely to be impacted? What levels of support do they need? These conversations help you prioritize the expenditures on your checklists.
Next, list every item you need to purchase as the business owner. Make sure you have enough lights, fans, and pumps. But, remember to also consider increased operational expenses (e.g., additional nutrients, media, scissors) to prevent production delays and accurately calculate Capex, margins, and profit.
Another tip is to constantly revisit your to-do list throughout the process. Keep tabs on progress and ensure everyone has an opportunity to ask questions and learn. Your team may also need to do some prep work, like pre-fabricating irrigation dripper lines or unboxing materials. For this reason, mutual understanding and collaboration are pivotal.
3. Account for Increased Needs
Vertical farming doubles, even triples, your production capabilities. Is your facility equipped to handle these changes?
Going multi-tier will significantly increase yields. Do you need to increase your curing capacity? The good news is solutions are readily available to optimize your curing space with mobile curing racks, purpose-built hangers, and airflow management solutions.
You will also need to consider your lighting options for your multi-tier racking as well as accessibility options and innovations that ensure the conditioned Co2-rich air that is delivered to the room is also delivered directly to the plants.
For example, Vertical Air Solutions’ In-Rack Airflow System is one of the best products for managing airflow in your vertical farm. With VAS 2.0, you can avoid the hassle of addressing stagnant air zones that frequently develop due to multi-tiered growing systems. Homogenizing leaf temperature on the bottom and top tiers (both at the front and back of the room) makes precision crop steering more achievable.
Below is a list of capacities to monitor while converting to a vertical farm:
- Electricity
- Water
- Nutrients
- Labor
- HVACD
4. Choose the Right LED Light
How will you light the top tier — hanging lamps from the ceiling or the racking? How big will your plants be at each stage? What PPFD are you hoping to achieve at each stage of growth? The answers to those questions will help you select the right wattage, spectrum, and fixture design to fit the space.
LED options for the modern cannabis cultivator are extensive. Thanks to their efficient output, slim design, and relatively low heat output it is easier than ever to find the right light to optimize plant growth at every stage.
While the performance of quality LED fixtures is no longer a question, you must still consider the mounting distance from the plant. Determine how much space the fixture needs to effectively accommodate in-rack airflow and plant growth.
LED lighting is a great fit for multitier cultivation as it is more controllable than HID lighting and capable of stimulating secondary metabolites, shortening production times, and reducing operational expenses (assuming your design and supporting equipment are set up for success).
5. Train Staff on Equipment, Ladder, and Scaffold Usage
Safety should always be a top priority in any operation. Vertical farms need to invest in solutions that prevent accidents, especially with employees tending higher-tier plants. Effectively training your team on navigating safety gates, ladders, and second-tier access ensures consistency, confidence, and employee well-being.
Host instructional meetings where employees can learn the dos and don’ts of vertical farming maintenance. Get feedback and adapt to obstacles as they arise. These exchanges help make sure everyone understands how to best use available tools to increase efficiency and prevent misuse.
Choosing a stable platform can also limit many safety concerns. Pipp’s ELEVATE® is designed to fit smoothly into Mobile Racking Systems, allowing growers to easily and quickly access upper-level tiers. This ergonomic design requires only one person to set up, thus helping reduce the risk of fatigue and injury.
6. Budget Accordingly
Last but certainly not least is budgeting. Yes, converting to and building a vertical farm requires an initial investment. Crunching numbers and signing checks can be daunting, but you see the opportunity to futureproof your facility and remain competitive for the long haul.
Going multi-tier isn’t just about increased canopy space and top-line revenue. Consider room utilization, grams per cubic foot, and production costs that fuel the operational efficiency and the phasing of your project. Taking advantage of utility incentives for your lighting, HVACD, and other electrical equipment can provide incentives to reduce capex and production costs while building a more valuable asset.
So, when budgeting for your project, be sure to consider your facility’s efficiency in addition to top-line revenue. This factor may help you determine how to allocate extra funds for retrofitting your current garden or building a future phase.
Use this checklist to assist you in budgeting for your vertical farm project:
- Start-up costs (e.g., contractor fees, equipment, lighting, etc.)
- Operational costs (e.g., electricity, labor, water usage, etc.)
- Equipment maintenance
- Production supplies
- Estimated profits
- Additional equipment and support needed to help plants flourish and your business thrive
Making the Switch With Pipp
Running a cannabis operation can be challenging in itself, and a complete overhaul can seem overwhelming. Whether you’re building a new facility or upgrading a pre-existing one, Pipp Horticulture can be your best resource when implementing a vertical farming system.
Pipp’s internal Grow Team has over 100 years of combined cultivation experience. We also work with some of the best industry consultants and have a vast network of vendor partners globally. We are here to provide our customers with unparalleled support before and after equipment installation.
Ready to get started? Contact us today for a consultation and more information on the benefits of vertical cannabis cultivation.
About the Guest Author
Since 2014, Robert Sandow, a cannabis consultant and writer, has been a notable figure in the cannabis cultivation industry. Having been born and raised on a farm in Kansas, Sandow brings a unique appreciation for small growers. He also values the importance of cultivating medicinal plants for the betterment of communities. His work has helped pioneer multi-tiered cannabis production.