9 Common Grow Room Problems to Avoid
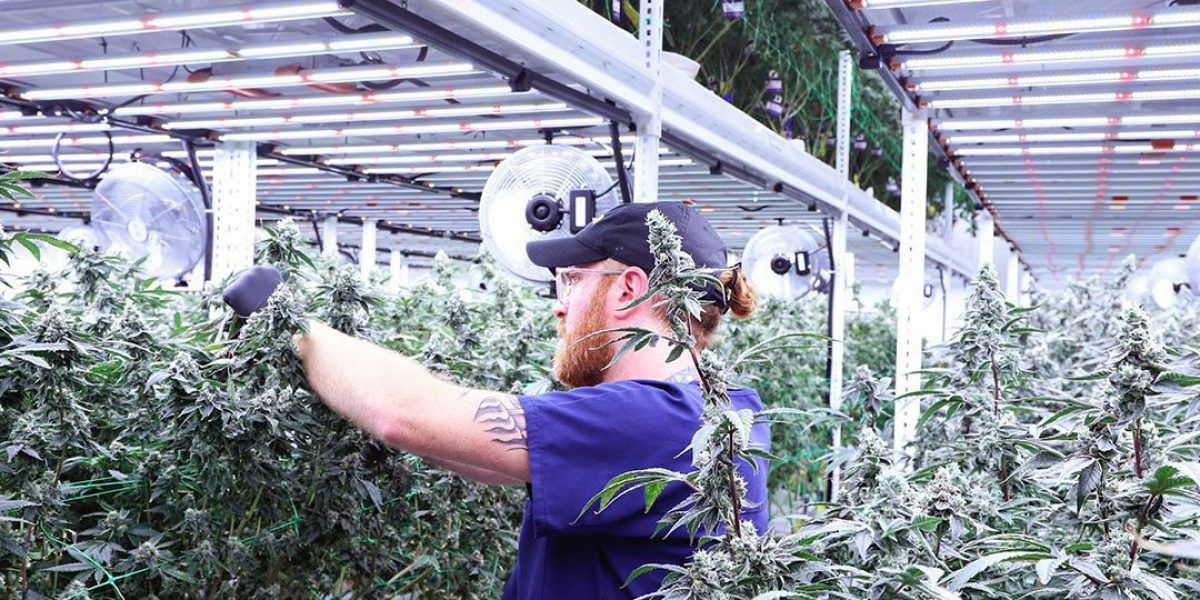
You’ll likely encounter a few setbacks when first entering the cannabis industry. Learning what does and doesn’t work for your business takes time. Still, having a basic understanding of best practices beforehand can help you avoid common cannabis growing problems.
You’ve invested so much into this space, and you want operations to run smoothly! So, how can you dodge the biggest pitfalls that can make or break grow room success?
We’re here to help you protect your investment by explaining 9 mistakes cannabis growers frequently make when getting started. Use this information to stay ahead of the competition and reap the benefits of a thoughtfully planned grow room.
Here are 9 common cannabis grow room mistakes to avoid:
1. Neglecting Utility Infrastructure
Plant count constantly changes as you develop as a business. However, the canopy footprint (or total bench area) is constant. Not understanding how much space you need to house your crop and accommodate expansion can cause substantial problems down the line.
Do your plants have enough space to move and develop freely? Is your veg room large enough to meet your flowering goals? Can you easily implement new equipment and technology based on your canopy footprint?
These questions should guide you as you plan a grow room. If you struggle with maximizing your space, mobile vertical grow-racking systems can help you gain square footage without sacrificing quality.
2. Neglecting Utility Infrastructure
Assuming your new property has enough power, gas, and water to run your multi-tier grow facility can cause delays.
For example, running too much equipment without adequate power can be hazardous. Dealing with electrical shocks and shorts can cost you valuable resources, yield, and time. Insufficient water flow can impair your ability to properly care for plants, ultimately impacting your entire operation.
3. Cutting Corners
4. Wasting Valuable Grow Space
One of your goals as a cultivator is likely to boost yield capabilities and profitability. Unfortunately, operating a single-tier growing platform cannot accommodate substantial expansion.
Cannabis needs room to grow, meaning horizontal square footage dictates how many plants you can cultivate. Not taking advantage of your entire vertical canopy footprint limits your facility’s potential to increase inventory, implement new equipment, or introduce additional strains.
5. Hiring the Wrong People
“You get what you pay for” is unequivocally true in the cannabis-growing industry. Don’t assume anyone can handle the fast-paced, intense, and hands-on workflow that comes with cannabis cultivation.
Potential hires can put whatever they want on their resumes–not checking their references or experience can mean dishing funds into more training or fixing their costly mistakes on the job. Even if they excelled at a smaller facility, can they manage thousands of plants as opposed to a few hundred?
6. Implementing Poor Environmental Controls
The initial costs of choosing reputable equipment can deter any grower, especially one who hasn’t yet turned a profit. However, long-term success is limited to good environmental controls.
A poor airflow design is perhaps one of the most common cannabis growing problems–practical and consistent air circulation is pivotal throughout the entire cultivation process. Ultimately, a shoddy airflow system can result in many cannabis growing problems, including mold, bud rot, delayed growth, disease, and even plant death.
7. Choosing Inefficient Lighting
High pressure sodium (HPS) technology can be inefficient at converting electrical energy into usable plant light. Moreover, removing HPS-generated heat requires more cooling capacity, which can be an additional expense when designing your grow room.
Alternatives like compact fluorescent lights (CFL) are inexpensive but power-hungry and short-lived. They are also generally only suitable for clones or seedlings. Ceramic discharge metal-halide (CDM) lamps provide a slightly better balanced light spectrum but are costly and unreliable.
Plants require various levels of light across development stages–your lighting layout and choices should account for these differences. Light exposure can dictate growth, flowering, and yield, so one mistake along the way can prove catastrophic to your crop.
8. Forgetting About Sanitization
Dirty facilities without proper reset and sanitization protocols increase the chance of disease, mold, pest infestations, and plant death. You also face the risk of failing regulatory lab tests.
For instance, poorly cleaned or neglected equipment can be breeding grounds for pathogens like pythium. These fungi can wreak havoc on roots before your plants have time to thrive. Furthermore, two-spotted spider mites can house themselves in unsanitized pots, only to reemerge once new seedlings are planted.
The worst feeling a cultivator can experience is failing a lab test or losing a harvest batch they just spent months growing.
9. Overlooking the Importance of Balance
Balance is the key to successful grow room design and operation. Are watering rates balanced with dehumidification capacity? Does your lighting align with CO2 levels?
Every system within your grow room works in harmony. If you just think about your fertilizer solution or irrigation strategy, you fail to recognize other parameters that disrupt this harmony.
Finding Solutions to Cannabis Growing Problems
Creating a cannabis grow room is a huge undertaking–missteps are normal and expected along the way. Still, you can limit the risk of unplanned expenses and setbacks by educating yourself and your team about common mistakes.
The Pipp Horticulture team can help you avoid these mistakes when growing cannabis. Pipp has a team of experts available to you with a combination of over 50 years of cannabis growing experience. We have engineered various cost-effective solutions to exponentially grow up to 5x more by maximizing cubic grow space and creating more efficient workflows.
Moving forward with Pipp Horticulture means working closely with our in-house professional engineers, CAD designers, sales support, and experienced cannabis operators. Let us help you maximize your production capability, reduce operating costs, and increase your overall revenue per square foot!
Here are a few ways to avoid falling victim to cannabis grow room mistakes:
- Run estimates: Estimates ensure you have a realistic overview of where you can allocate funds, whether to expansion or essential changes (e.g., purchasing new equipment). This data can limit delays, meaning you can get to work faster.
- Connect with local services: Engage with your local utility providers to estimate the timeline and cost of upgrading your facility to meet demand.
- Start out on the right foot: You must invest in efficient technologies to survive in today’s indoor cannabis market. For example, vertical farming can have a higher upfront cost. However, this asset sets you up for success with a lower production cost.
- Vet potential employees and partners: Investing in the right team will pay off in the long run! Engage experienced consultants, architects, engineers, and contractors specializing in building an indoor cannabis facility. Connect with the Pipp Horticulture team when considering a team!
- Choose multi-functional solutions: The patented Vertical Air Solutions (VAS) system is designed to work with an HVAC system specified for vertical farm size and growing methods. The VAS system lets you control environmental factors such as temperature, humidity, airflow velocity, and CO2 levels, optimizing plant health and finished product quality.
- Build up: Multi-tier farming may have a higher upfront cost. Still, the ability to produce more products in a smaller overall footprint is inherently more efficient and cost-effective.
- Simplify sanitation: Save yourself time and energy by using equipment designed to stay clean. Pipp Grow Racks have an E-Coat base and a powder coat top layer, providing antimicrobial and anti-fungal effects.